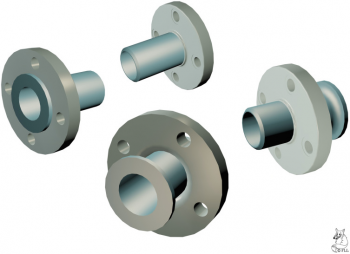
Image Source: Science Direct
Pipe flanges
Pipe Flanges are the projecting edges, rims, ribs, or collars that join two pipes or a pipe to a fitting or piece of equipment. For situations when solvent cementing would not hold, such as during the dismantling of a piping system or during a temporary or mobile installation, or when two materials have to transition into one another, pipe flanges are utilized.
Flanges also have a high moment-carrying capability in comparison to other types of mechanical connections. This is a crucial quality for systems vulnerable to pipe-walking and lateral bending due to changes in temperature and pressure (e.g. deep water lines).
Mechanical joints vs Flange pipe
The most common application for mechanical joints is in an underground pipe, valve, and fitting connections. When in the retrained position, the mechanical joint’s retention gland utilizes a wedge action to keep the joint in place. When the gland is squeezed against the bell, it wedges the gasket and creates a leak-proof seal.
Mechanical Joints Advantages
- There is zero structural or thermal change to the parts
- Options galore for the raw stuff
- Superior strength and endurance
- Possibility of material movement after merging
- Simple Quality Management
- Environmentally responsible, emitting no pollutants
Mechanical Joints’ Disadvantages
- Joint repair is very challenging and sometimes impossible
- Can be costly due to more rivets required
- The cost would be too high to justify using it in the open air
The flange creates a firm, non-deflecting joint. This is bad for subterranean installations that change often. The ground movement might compromise joint integration. Tightening the bolts and squeezing the gasket creates a watertight seal.
Flanges’ Advantages
- Painting and blasting aren’t essential but are often specified
- Threaded connections may not need hot work permits
- If needed, many pipe spools may be supplied freely
Flanges’ Disadvantages
- Insulating flanged pipes are costly
- Flanged pipes need more room
- Leaky flange connections
Flange marking & labeling
If you want have marks and labels on your flange, first, decide on a labeling scheme. Then, learn about the labeled piping system. How many types of pipelines convey what materials? Last, publish the labels. For typical materials, you may buy pre-printed labels or utilize a custom label printer at work.
Types of pipe flanges
Pipe flanges are second only to welding as a means of putting pipes together. When disassembling a joint, these are the tools of choice. Having this option means more freedom in terms of routine upkeep. Therefore, it is appropriate to choose the appropriate flanges.
You can also check out the following video for more information.
Acquire the most accurate flanges which is convenient for daily use and commercial use
Socket Welding Flange
Image Source: Marcel Piping
In the high pressure pipe industry, socket-weld flanges are primarily utilized on smaller diameter pipes. The pipe is inserted into the flange’s socket end, and fillet weld is applied around the flange’s top. As a result, the pipe’s interior is smoother, allowing for more efficient transport of the gas or liquid being transported.
Throw on the diameters of the hubs on pipe flanges, which are the standard, may be anywhere from 1/2 inch to 24 inch. Socket Weld pipe flanges are offered by Coastal Flange in every conceivable size, grade, and detail.
In addition, Socket Welding Flange depending on the application may have:
- Raised face,
- Flat face
- RTJ facing
Under 400#, socket weld pipe flanges with raised faces are typically 1/16 inches tall. Raised face heights of 1/4″ are the norm for socket weld pipe flanges in the 400# class and above.
Slip on flange
Image Source: Savree
SO flange is short for slip on flange. Flanges with a SO thread are designed to be somewhat larger on the inside than the pipe they are meant to cover. A fillet weld at the top and bottom of the flange allows them to attach to the pipe.
Flanges have an inner diameter that is slightly larger than the pipe’s outer diameter, allowing the two to be joined through lap welding at the flange’s top and bottom.
Slip on Flange Specifications:
- Common exterior diameters range from 1/2 in. to 24 in.
- Custom-made exterior diameters as large as 60 inches.
- Classifications go from 150 to 300 to 600 to 900 to 1500 to 2500 pounds. Ranging from around a PN2.5 to a PN250.
- RF (Raised Face) Flanges, RTJ Flanges (Ring Type Joint)
Some advantages:
- Low installation costs
- Less time spent aligning pipes and cutting them into size.
Weld Neck Flange
Image Source: Forged Components
A pipe may be welded to a welding neck flange (“WN”) that has a long, tapered hub. This kind of flange is often utilized in high-pressure and high-/low temperature applications that call for an unhindered flow of the fluid being transported by the piping system.
The weld neck flange and pipe are mechanically stressed in a uniform manner thanks to the tapered hub, which also makes it easier to conduct radiographic inspections to look for any leaks and welding flaws. A single fully penetrated V-shaped butt weld joins a welding neck flange to a pipe.
Things to consider while buying a weld pipe flange:
- Fabrication requires a high level of competence.
- Due to the lengthy hub, the piping system needed additional room to handle it.
- All sizes of weld neck flanges are offered, and they come in FF, RF, or RTJ types.
- The pipe-welded Weld Neck flange is visible.
Threaded Flange
Image Source: Ingenio Virtual
Threads on the flange allow it to be screwed into a pipe, thus the name “threaded” or “screwed” flange.
Threaded flanges come in a wide range of diameters and pressure ratings, however they are typically only utilized for smaller pipe systems ( 4 inches). In addition, it is normally only used in non-toxic, low-pressure, low-temperature environments. Most threaded flanges are between 1/2 and 2 inches in diameter, although larger sizes are becoming prevalent.
Threaded flanges only have two possible faces—flat and raised—because they are used in lower-pressure settings. Due to distortion of the thread geometry at high temperatures, they cannot be used in situations where leakage is a concern.
Advantages:
- Flanges with threads allow a pipe to be attached without the need of welds.
- Faster and less cumbersome in assembly and breakdown
Disadvantages:
- Not suitable for use in conditions when the temperature is really high
- unsuitable for pipelines that have thin walls
Blind Flange
Image Source: Hard Hat Engineer
A blind flange, also known as a non-hub flange, is a flange which does not have a hub or a bored center. Blind flanges are comparable to regular flanges in that they share the same bolting pattern, face type, and thickness. Blind flanges may also be employed to seal a pressure vessel’s nozzle opening.
Blind flanges have widespread use in the petrochemical, pipe engineering, public services, and water works industries. It’s helpful for fixing a pipeline farther upstream. Actually, a blind flange may be included into the completed pipeline as part of the building process. Simply by connecting to the end flange, the pipeline may be extended or expanded.
A few benefits:
- There is a direct correlation between the pressure and wear between flange surfaces and the design structure.
- The blind flange is functioning in a dirty or dusty environment.
- The system is reliable and simple to keep up.
Expander Flange
Image Source: Micron Steel
Flanges with expandable hubs are called “expander flanges,” and they resemble weld neck flanges in appearance but have much larger diameters (one or two sizes). The large stress concentrations at the flange’s base may be mitigated thanks to its design, which transfers the stresses to the pipe. It expands the pipe diameter at the flange joint.
Additionally, the expander flanges may be utilized to connect piping to other devices including compressors, pumps, and controls.
Some benefits of expander flanges:
- Comparatively small to a reducer-welding neck flange
- Expander Flange just needs one butt-weld
- Very competitively priced
- More Sizes available
Flangeolet / Weldoflnage/ Nippoflange
An olet (often a weldolet or nipple) is joined with a flange to form a flangeolet. High pressure pipe utilizes a 90-degree branch connection.
Two weld joints are cut down to one, which is a significant improvement over the standard Olet + Pipe + Flange connection.
Specialty flange
Reducing flange
Image Source: JF Engineering
When the diameter of a pipe has to be reduced, a flange of the appropriate size must be used. Flange (dimensions) often correspond to bigger NPT pipe size; bore (dimensions) typically correspond to smaller pipe size (NPT). Blind, slip-on, threaded, and weld neck flanges are the most common types of these flanges.
Uses of Reducing Flanges:
- Reducing flanges are used to join two pipes together.
- When compared to non-reducing flanges, reducing flanges are somewhat simpler to bolt together.
- Flanges of varying sizes may be joined together with the utmost ease thanks to this ingenious product.
- There is a wide variety of sizes and pressure ratings for these flanges to choose from.
- Flanges of identical diameters equipped with various connecting parts are welded, glued, or clamped together to create a reducing flange.
- Using them to join flanges of various sizes is the quickest, cheapest, and easiest solution available.
Other flange design considerations
Flange diagram
Image Source: Flowstar
From 15mm (1/2″) to 600mm (24″), these tables have flanges of all sizes (24″). These flange tables include the most popular flange standards, such as ANSI, PN, and the outdated British BS10 Table D through K. Valves are commonly connected to pipes using flanges because they allow for quick and simple removal when repair is required.
Flat (often cast iron or ductile iron) or raised face flanges are both acceptable within the same specification (commonly cast steel and stainless steel). Important flange measurements are included in these tables so that you may determine which kind of flange you have.
By flange Materials
It’s common practice for manufacturers to produce pipe flanges in a variety of materials and quality levels. Producing Flanges may be done using a wide variety of materials.
Pipe flanges are often made from the following:
- nickel alloys
- Inconel
- Incoloy
- Hastelloy
- Monel
- carbon steel
- high yield carbon steel
- alloy steel
- stainless steel
- duplex and super duplex
In choosing the right flange, consider these three materials:
Carbon Steel
Carbon steel is fatigue-resistant, strong, chemically resistant, robust, and resistant to stress-corrosion cracking. This makes Flanges suitable for joining pipelines and supporting mechanical pieces.
Alloy Steel
Alloy steel contains more chromium and molybdenum than carbon. It can handle tremendous pressure and heat. It has better corrosion resistance than carbon steel grades.
Stainless Steel
Nickel, Chromium, and Molybdenum distinguish stainless steel from other materials. Stainless Steel is frequently utilized and resists corrosion. This material may be used to make Pipe Flanges of various sizes.
By flange face types
The plain/flat flange, the raised flange, and the ring-type junction are the three most prevalent kinds of flange faces (RTJ).
Flanges with a flat face (FF) need a soft gasket made of a material other than metal, and their sealing surface must be serrated. Low-pressure applications, such as pressure classes 125 and 250, are ideal for this flange design.
RF flanges differ from standard flanges in that their sealing faces project outward from the bolting circle plane in a circular form. All pressure classes, and therefore a broad variety of pressure and temperature ratings, are covered by the availability of raised face flanges.
Flanges with a ring-type junction (RTJ) are a modification of the raised face flange. In more demanding situations, such as those involving high pressure and/or high temperature (>7500C / 1,3820F), RTJ flanges are the norm. Class 900 and beyond is where they really shine.
By flange class ratings
Class, poundage, or even simply a number followed by an octothorpe (the # symbol; the hashtag for you millennials; the pound sign for everyone else) are common ways to refer to different types of pipe flanges.
In reference to a flange’s pressure rating, these words are all equivalent. To add more confusion, a flange rated at 600 pounds does not always have a 600 pound pressure rating.
Instead of “pounds per square inch,” the current nomenclature for flange pressure classes is “pounds.” Always remember that the words “pound” and “class” may be used interchangeably when discussing the pressure class of flanges.
Class 150, 300, 400, 600, 900, 1500, and 2500 are the corresponding weight classes. Generally speaking, a flange with a higher rating will be heavier and able to handle more pressure and temperature. So, for a particular material, the maximum allowed pressure decreases as the temperature increases, and vice versa.
By flange Standards, Dimensions
Image Source: Savree
Standardizing the size of the different flange types based on needs, i.e. the service conditions they are expected to meet, was required in the same way as piping was. Additionally, standardization allows for less complicated and error-prone communication between designers, manufacturers, and others involved.
Valve end Connections
Flanged pipe fittings
A pipe “flange” is a metal ring that is welded onto the end of a pipe and has multiple bolt holes drilled into it perpendicular to the axis of the pipe.
The donut-shaped gasket is inserted between the flange pairs before the bolts are tightened, creating a pressure-tight junction. Xhval industrial valve co.ltd manufactures flanged valves and also produces gaskets from materials that are more pliable than the flange material. As the gasket is “crushed” between the flanges, it effectively seals any gaps.
Flanged end valves
Image Source: India Mart
Flange end ball valves are used to control the flow of a pipeline and maintain a constant pressure throughout the system or operation. It is equipped with a spherical disc that may be opened or closed to regulate fluid flow
Flanged ball valves
Image Source: Xhval
It’s a ball valve, which is a popular kind. Ball valves of this design find use in many other fields.
Flanged global valves
Image Source: Xhval
Without the need for any specialized machining, the globe valve may be set up or taken down in no time.
Flanged check valves
Image Source: Xhval
Flanged check deals with gas and petroleum as well as transportation. It is also used in the production of electricity.
Flanged valve end connection VS. other valve end connections
Threaded connections
Image Source: HMA Group
Valves that include threading on the inside or outside of the valve body are known as threaded valves or internal threaded valves. Internal threaded valves and exterior threaded valves are the two primary categories. A NPT valve or screwed end valve is also considered as a threaded valve.
Soldered ends
Image Source: Jomar Valve
The connection between a ball valve and a copper pipe is leak-proof after being soldered. After heating the valve and pipe ends to the proper temperature, the plumbing solder dissolves into the connection by capillary action, creating a watertight seal once it cools.
Glue socket
Image Source: eBay
Connections made using glue are also known as FIP connections, slip-fit connections, friction fits, pipe ends, and spigots. Basically, they can be summed up in a single sentence. Glue socket connections are made by inserting a pipe with an outer diameter that is only a hair bigger than the socket’s inner diameter.
Npt end connections
Image Source: Amron International
Tapered threads, as seen on pipes and fittings, conform to this American standard. A taper thread, as opposed to a bolt’s straight threads, will draw tight and provide a leak-proof seal. Threads should be sealed with pipe tape or pipe compound to prevent leaks.
Wafer end connections
Image Source: IndiaMart
Due to their diminutive stature, butterfly valves are almost exclusively fitted with wafer-style flange connections. But they are also available on certain brands of ball valves. This kind of attachment entails squeezing the valve between two flanges with the use of long bots or threaded end rods.
Socket weld ends
Image Source: Quality Manufacturer of Industrial Pipe Fittings
Socket welds are an attachment method for pipes that include fitting the pipe into a depression on a gate valve, fitting, or flange. Socket Weld fittings are preferred over buttweld fittings for smaller pipe diameters (Small Bore Piping), specifically piping with a nominal pipe size (NPS) of 2 or less.
Conclusion
Flanges come in a wide variety of types, textures, temperatures, shapes, sizes, and functions, making it tough to choose the best one for your house. Doing some preliminary reading is often the simplest method for newcomers to figure out which option is going to work best for them. Discovering their sizes and specs might also lead to fresh perspectives.